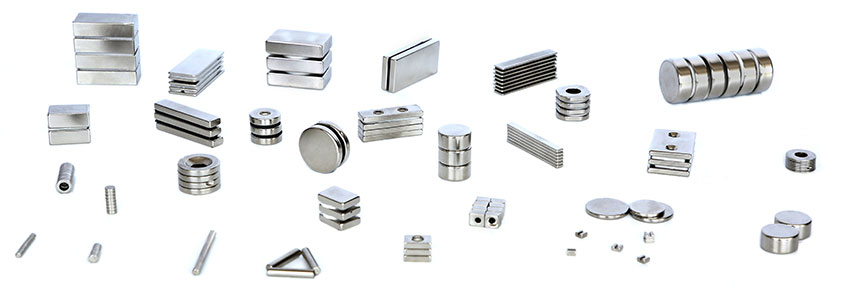
Neodymium Magnet (also known as NdFeB Magnet, Neo Magnet, Strong Magnet, Permanent Magnet, Rare Earth Magnet) is one of the most widely used type of rare-earth magnet.
Neodymium magnet is a permanent magnet made from an alloy of neodymium, iron, and boron to form the Nd2Fe14B tetragonal crystalline structure. Developed independently in 1984 by General Motors and Sumitomo Special Metals,neodymium magnets are the strongest type of permanent magnet available commercially.
Because of different manufacturing processes, they are divided into two subcategories: sintered NdFeB magnets and bonded NdFeB magnets.
Neodymium magnets are powerful yet discreet magnets, providing a far greater magnetic hold than other magnets at a fraction of the size.
They are particularly suitable for high volume production in the variety of shapes and sizes. Precise dimensional control can be obtained in the machining processes. With these advantages, Neodymium magnets have been widely applied in lots of commercial fields, such as high-performance motors, brushless DC motors, magnetic separators, magnetic resonance imaging (MRI), sensors, loudspeakers, consumer electronics and green energy.
Our range of rare earth neodymium magnets is made up of an array of shapes and sizes to facilitate multiple uses, including but not limited to holding and hanging functions and closure applications.
Neodymium magnets are all graded by the material they are made of. As a very general rule, the higher the grade (the number following the ‘N’), the stronger the magnet. The highest grade of neodymium magnet currently available is N52. Our standard stock neodymium magnets are graded at N35, this is the most cost effective rating for use in retail displays, exhibitions and closures.Any letter following the grade refers to the temperature rating of the magnet. If there are no letters following the grade, then the magnet is standard temperature neodymium. The temperature ratings are standard (no designation) – M – H – SH – UH – EH.
All our neodymium magnets are finished with a triple coating of nickel-copper-nickel to prevent corrosion and provide optimum performance up to 60°C.
Rare Earth Magnets have a high resistance to demagnetization, unlike most other types of magnets. They will not lose their magnetization around other magnets or if dropped. They will however, begin to lose strength if they are heated above their maximum operating temperature, which is 176°F (80°C) for standard N grades. They will completely lose their magnetization if heated above their Curie temperature, which is 590°F (310°C) for standard N grades.
We can supply higher rated magnets for special applications, including magnets for use in high temperature environments, which can withstand higher temperatures without losing strength.
We can make neodymium magnets into various shapes like disc magnet, block magnet, cube magnet, ring magnet, rod magnet, tile magnet, sphere magnet, and etc.
We can make shiny neodymium magnets to our customers by different coating including Zinc, Nickle-Copper-Nickle, Silver, Gold, Epoxy, etc.
We can also custom manufacture neodymium magnets to fit your exact specifications, just contact us today, and we’ll work with you to determine the most economical solution for your project.
Properties of Sintered Neodymium Magnets
Grade | Remanence | Coercive Force | Intrisic Coercive Force | Max Energy Product | Working Temp(L/D=0.7) | ||||
KGS | T | KOe | KA/m | KOe | KA/m | MGOe | KJ/m3 | ℃ | |
N30 | 10.8-11.3 | 1.08-1.13 | ≥10 | ≥796 | ≥12 | ≥955 | 28-31 | 223-247 | ≤80 |
N33 | 11.3-11.8 | 1.13-1.17 | ≥10.5 | ≥836 | ≥12 | ≥955 | 31-34 | 247-271 | ≤80 |
N35 | 11.7-12.2 | 1.17-1.22 | ≥10.9 | ≥868 | ≥12 | ≥955 | 33-36 | 263-287 | ≤80 |
N38 | 12.2-12.5 | 1.22-1.25 | ≥11.3 | ≥899 | ≥12 | ≥955 | 36-39 | 287-310 | ≤80 |
N40 | 12.5-12.8 | 1.25-1.28 | ≥11.4 | ≥907 | ≥12 | ≥955 | 38-41 | 302-326 | ≤80 |
N42 | 12.8-13.2 | 1.28-1.32 | ≥11.5 | ≥915 | ≥12 | ≥955 | 40-43 | 318-342 | ≤80 |
N45 | 13.2-13.8 | 1.32-1.38 | ≥11.6 | ≥923 | ≥12 | ≥955 | 43-46 | 342-366 | ≤80 |
N48 | 13.8-14.2 | 1.38-1.42 | ≥11.6 | ≥923 | ≥12 | ≥955 | 46-49 | 366-390 | ≤80 |
N50 | 14.0-14.5 | 1.40-1.45 | ≥10 | ≥796 | ≥12 | ≥955 | 48-51 | 382-406 | ≤80 |
N52 | 14.3-14.8 | 1.43-1.48 | ≥10 | ≥796 | ≥12 | ≥955 | 50-53 | 398-422 | ≤80 |
35M | 11.7-12.2 | 1.17-1.22 | ≥10.9 | ≥868 | ≥14 | ≥1114 | 33-36 | 263-287 | ≤100 |
38M | 12.2-12.5 | 1.22-1.25 | ≥11.3 | ≥899 | ≥14 | ≥1114 | 36-39 | 287-310 | ≤100 |
40M | 12.5-12.8 | 1.25-1.28 | ≥11.6 | ≥923 | ≥14 | ≥1114 | 38-41 | 302-326 | ≤100 |
42M | 12.8-13.2 | 1.28-1.32 | ≥12.0 | ≥955 | ≥14 | ≥1114 | 40-43 | 318-342 | ≤100 |
45M | 13.2-13.8 | 1.32-1.38 | ≥12.5 | ≥995 | ≥14 | ≥1114 | 43-46 | 342-366 | ≤100 |
48M | 13.8-14.3 | 1.38-1.43 | ≥12.9 | ≥1027 | ≥14 | ≥1114 | 46-49 | 366-390 | ≤100 |
50M | 14.0-14.5 | 1.40-1.45 | ≥13 | ≥1033 | ≥13.5 | ≥1075 | 48-51 | 382-406 | ≤100 |
52M | 14.2-14.7 | 1.42-1.47 | ≥13 | ≥1033 | ≥13 | ≥1035 | 49-53 | 390-422 | ≤100 |
35H | 11.7-12.2 | 1.17-1.22 | ≥10.9 | ≥868 | ≥17 | ≥1353 | 33-36 | 263-287 | ≤120 |
38H | 12.2-12.5 | 1.22-1.25 | ≥11.3 | ≥899 | ≥17 | ≥1353 | 36-39 | 287-310 | ≤120 |
40H | 12.5-12.8 | 1.25-1.28 | ≥11.6 | ≥923 | ≥17 | ≥1353 | 38-41 | 302-326 | ≤120 |
42H | 12.8-13.2 | 1.28-1.32 | ≥12.0 | ≥955 | ≥17 | ≥1353 | 40-43 | 318-342 | ≤120 |
45H | 13.2-13.7 | 1.32-1.37 | ≥12.1 | ≥963 | ≥17 | ≥1353 | 43-46 | 342-366 | ≤120 |
48H | 13.7-14.3 | 1.37-1.43 | ≥12.2 | ≥971 | ≥17 | ≥1353 | 46-49 | 366-390 | ≤120 |
50H | 13.9-14.5 | 1.39-1.45 | ≥13 | ≥1035 | ≥17 | ≥1353 | 47-51 | 374-406 | ≤120 |
33SH | 11.3-11.8 | 1.13-1.18 | ≥10.6 | ≥844 | ≥20 | ≥1592 | 31-34 | 247-271 | ≤150 |
35SH | 11.7-12.2 | 1.17-1.22 | ≥11.0 | ≥876 | ≥20 | ≥1592 | 33-36 | 263-287 | ≤150 |
38SH | 12.2-12.5 | 1.22-1.25 | ≥11.4 | ≥907 | ≥20 | ≥1592 | 36-39 | 287-310 | ≤150 |
40SH | 12.5-12.8 | 1.25-1.28 | ≥11.8 | ≥939 | ≥20 | ≥1592 | 38-41 | 302-326 | ≤150 |
42SH | 12.8-13.2 | 1.28-1.32 | ≥12.4 | ≥971 | ≥20 | ≥1592 | 40-43 | 318-342 | ≤150 |
45SH | 13.2-13.7 | 1.32-1.37 | ≥12.3 | ≥995 | ≥20 | ≥1592 | 43-46 | 342-366 | ≤150 |
48SH | 13.7-14.2 | 1.37-1.42 | ≥12.5 | ≥995 | ≥20 | ≥1592 | 45-49 | 358-390 | ≥150 |
28UH | 10.2-10.8 | 1.02-1.08 | ≥9.6 | ≥764 | ≥25 | ≥1990 | 26-29 | 207-231 | ≥180 |
30UH | 10.8-11.4 | 1.08-1.14 | ≥10.2 | ≥812 | ≥25 | ≥1990 | 28-32 | 223-254 | ≤180 |
33UH | 11.3-11.8 | 1.13-1.18 | ≥10.7 | ≥852 | ≥25 | ≥1990 | 31-34 | 247-270 | ≤180 |
35UH | 11.7-12.2 | 1.17-1.22 | ≥10.8 | ≥860 | ≥25 | ≥1990 | 33-36 | 263-287 | ≤180 |
38UH | 12.2-12.5 | 1.22-1.25 | ≥11 | ≥876 | ≥25 | ≥1990 | 36-39 | 287-310 | ≤180 |
40UH | 12.5-12.8 | 1.25-1.28 | ≥11.5 | ≥915 | ≥25 | ≥1990 | 38-41 | 302-326 | ≤180 |
42UH | 12.8-13.2 | 1.28-1.32 | ≥12.2 | ≥971 | ≥24 | ≥1911 | 39-43 | 310-342 | ≤180 |
28EH | 10.4-10.9 | 1.04-1.09 | ≥9.8 | ≥780 | ≥30 | ≥2388 | 26-29 | 207-231 | ≤200 |
30EH | 10.8-11.4 | 1.08-1.14 | ≥10.2 | ≥812 | ≥30 | ≥2388 | 28-32 | 223-255 | ≤200 |
33EH | 11.3-11.8 | 1.13-1.18 | ≥10.3 | ≥820 | ≥30 | ≥2388 | 31-34 | 247-270 | ≤200 |
35EH | 11.7-12.2 | 1.17-1.22 | ≥10.5 | ≥836 | ≥30 | ≥2388 | 33-36 | 263-287 | ≤200 |
38EH | 12.2-12.5 | 1.22-1.25 | ≥11.5 | ≥915 | ≥30 | ≥2388 | 35-39 | 279-310 | ≤200 |
Neodymium Magnets Physical Properties & Application to Environment of the Coating
Coating Material | Surface Colour | Properties | Environment of Application | Thickness of Coating layer |
Zine | Blue, Black and rainbow etc | Compact, Stable and Homogeneous | With reasonalbe capability of anticorrosion | 6um≤∮≤12 |
Nickel-Copper-Nickel | White and black | Light and Stable | Suitable for higher corrosive environment | 15μm≤∮≤30pm |
Phosphorization | Colorless or light gray | uniform thickness | short-term anticorrosion | |
Epoxy | Black and Gray | layer with certain luster, insurability | Suitable for higher corrosive environment | ≥15μm |
Parylene | transparency | uniform thickness, density pinholes-free and insurability | Excellent capability of anticorrosion especially for small items | 0.1μm≤∮≤100pm |
Ni+Cu+Epoxy | Black | Layer with certain luster | salt spray resistance>300hr | 10-30μm |
insurability and stability | Excellent capability of | |||
anticorrosion. Suitable for | ||||
hostile environment | ||||
salt spray resistance>300hr |